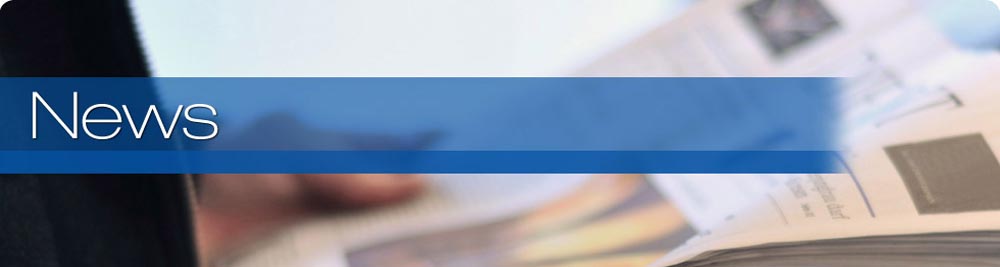
Die-casting Introduction
Die casting is a versatile process for producing engineered metal parts by forcing molten metal under high pressure into reusable steel molds. These molds, called dies, can be designed to produce complex shapes with a high degree of accuracy and repeatability. Parts can be sharply defined, with smooth or textured surfaces, and are suitable for a wide variety of attractive and serviceable finishes.
Die cast parts are important components of products ranging from automobiles to toys. Parts can be as simple as a sink faucet or as complex as a connector housing.
Die-casting materials
The main die casting alloys are: zinc, aluminium, magnesium, copper, lead, and tin. Specific dies casting alloys include: ZAMAK, zinc aluminum, AA 380, AA 384, AA 386, AA 390, and AZ91D magnesium.The following is a summary of the advantages of each alloy:
Zinc: the easiest alloy to cast; high ductility; high impact strength; easily plated; economical for small parts; promotes long die life.
Aluminum: lightweight; high dimensional stability for complex shapes and thin walls; good corrosion resistance; good mechanical properties; high thermal and electrical conductivity; retains strength at high temperatures.
Magnesium: the easiest alloy to machine; excellent strength-to-weight ratio; lightest alloy commonly die cast.
Copper: high hardness; high corrosion resistance; highest mechanical properties of alloys die cast; excellent wear resistance; excellent dimensional stability; strength approaching that of steel parts.
Lead and Tin: high density; extremely close dimensional accuracy; used for special forms of corrosion resistance.
Maximum weight limits for aluminium, brass, magnesium, and zinc castings are approximately 70 pounds (32 kg), 10 lb (5 kg), 44 lb (20 kg), and 75 lb (34 kg), respectively.